STOP FIGHTING A LOSING QA BATTLE
Juni 03, 2021
The opportunities presented by Autonomous Machine Vision
The book Thinking, Fast and Slow by Nobel laureate Daniel Kahneman addresses the unconscious biases that influence human decision making. One example is the sunk cost fallacy, which gives us a stubborn allegiance to prior investments.
Here I will discuss the limitations of traditional machine vision for quality assurance (QA).The sunk cost fallacy compels people to make continued investments in bad stocks, businesses or technology, purely because they’ve already paid for it. When faced with a choice to make additional investment, its often instinctive to justify a failing endeavour, which can impact the way new opportunities are regarded. The problem is that we can be left with unfulfilling or costly results, because inherent bias has prevented us from evaluating new opportunities fairly.
When investing in new machine vision technology for QA, a manufacturer should approach their options with an open mind. Across the industry, manufacturers have implemented traditional machine vision technology to identify defective products on their line – and rightly so.
Once a QA manager has weighed up the cost of implementing a machine vision solution and decided that it is worthwhile, they will contact an integrator to take the project through the next steps. The integrator will create Proof of Concepts, develop a potential solution, test it and optimize it. Once the solution components have been decided on, the integrator will purchase them and then build the cameras, lenses, lighting, housing, communications and interfaces into a hard-engineered machine vision solution on the production line.
The process of building a traditional machine vision solution will typically cost the manufacturer between €20,000 to €150,000. Only once the investment is made, the time has been spent and production been halted, can the manufacturer begin to benefit from visual QA.
Once the manufacturer has invested in a solution, it is fixed to its original position. This means that if there is a change in the environment, such as an alteration in lighting, in the product inspected, or in the line itself, the system will not, and cannot, self-adapt. Similarly, the QA solution cannot be just moved to a different point or product on the production line to comply with its changing needs. The easiest approach in such situations would be to return to the systems integrator and request that they adjust the existing solution to meet the new conditions, or quite often – scrap the old solution, and build a new one altogether. The bottom line is, the manufacturer is dependent on the integrator’s expertise to cope with any change.
New opportunities
Fortunately, there is now an alternative. Advances in electro-optics, artificial intelligence and other technologies have enabled the development of Autonomous Machine Vision.The technology consists of a single appliance that can be applied to any point of a production line in minutes. It is standalone and simple to install by the manufacturer’s personnel without the need to involve an integrator. The immediacy and affordability of Autonomous Machine Vision QA also means that the manufacturer can implement visual QA systems at a fraction of the cost and time of traditional solutions.
Because it is self-setting, self-learning and self-adjusting, Autonomous Machine Vision systems can be quickly and easily moved from one point of a production line to another. Using just a few good samples, the system will be ready to inspect any incoming product and identify those containing a defect. QA managers have full control and full flexibility, as they can easily take complete responsibility for their visual inspection tasks.
Letting go of the sunk cost fallacy thus allows manufacturers to reap the benefits of Autonomous Machine Vision. Manufacturers now have the option to leave behind the high costs, long wait times and downtime of traditional machine vision. As the American cartoonist Charles Schulz once said, “no problem is so formidable that you cannot walk away from it.”
You May Also Like
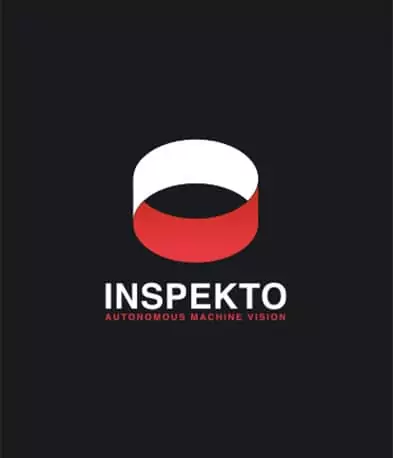
MACHINE VISION: CUTTING THE COST
New technology is changing the machine vision business model. Kakeibo is the Japanese art of saving money. The concept, invented in 1904, involves keeping a budgeting journal to…
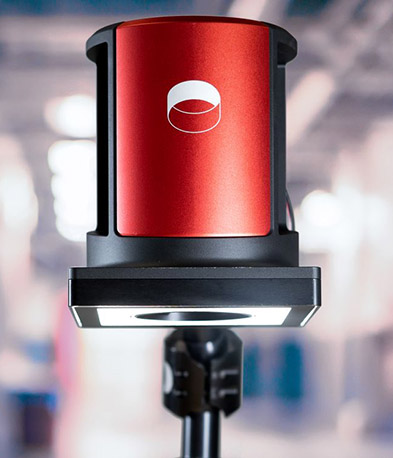
THE POISONED APPLE EFFECT
Breaking the chains of Traditional Machine Vision. In Snow White and the Seven Dwarfs, the jealous stepmother of the protagonist orders the title character to be killed. Snow…
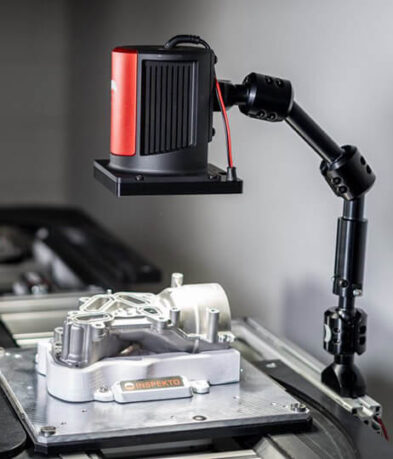
DEFINING AUTONOMOUS MACHINE VISION – A NEW CATEGORY
Industrial manufacturing will never be the same. “You never change things by fighting the existing reality. To change something, build a new model that makes the existing model…